Continued from the previous article "How to maintain, clean and repair the fermenters? [Part 1]"
Routine maintenance:Check the operation of the stirring shaft, the heat of the motor and abnormal noise frequently, and check the relevant bolts frequently for looseness.
Check the wear of oil seal and carbon brush of motor, as well as the wear of oil seal and bearing every year
Routine maintenance:
It is important to ensure that the steam pressure is constant during use. Steam filter cartridge will also be clogged after a period of use, and the cartridge needs to be replaced. During operation, do not open all steam valves at the same time. This will impact the steam filter element, which will seriously break or leak the element and make it fail.
Put the electrode in vertical position and unscrew the old electrode film. Rinse the inner electrode body with water and dry it carefully with cotton paper. Check that there is no electrolyte between the inner electrode body and the stainless steel housing. If there is any residual electrolyte, shake it off gently.
After using for a period of time, if you find that the electrode body silver ring is black, you can use 1000 mesh or more fine sandpaper to polish.
Check O-rings and springs for mechanical damage and replace if needed.
Pour the electrolyte into the membrane to be replaced, with the liquid level controlled below the threads. Adding more electrolyte appropriately can avoid affecting the electrode polarization due to less electrolyte.
Place the electrode in vertical position and screw the membrane gently onto the electrode, pay attention to the principle of "Advance one, retreat two" when screwing the electrode membrane to avoid the membrane being burst due to the excess liquid in the membrane not being discharged in time.Finally the electrode film should be tightened until no O-ring seal color is exposed and the oozing electrolyte is dried with cotton paper.The membrane will be easily tightened due to the sealing effect of the O-ring. If you need to screw it hard or if the process cannot be done easily, it may not be screwed in the correct position.
The electrodes must be repolarized and calibrated after each membrane or electrolyte change (see operating instructions for details).
Fault determination, cooling valve failure:
- Maintenance of mixing system
Routine maintenance:Check the operation of the stirring shaft, the heat of the motor and abnormal noise frequently, and check the relevant bolts frequently for looseness.
- Regular maintenance
Check the wear of oil seal and carbon brush of motor, as well as the wear of oil seal and bearing every year
- Maintenance and servicing of sterilized air systems
Routine maintenance:
- Need to pay attention to the operation of the air compressor, in the fermentation process should be drained twice a day to the air storage tank drain valve.
- Filter maintenance and servicing sterilization temperature should be controlled below 125°C.
- Because the filter material is too high temperature, the binder will come off and make the filter fail.
- Replacement off filter element
- As the air contains a lot of dust, the filter will gradually block the micro-pores of its element after a period of time, which leads to an increase in resistance on the one hand, causing a serious shortage of air flow and an increase in air pressure drop, thus affecting the ventilation capacity, and at the same time may cause bacterial contamination. At this time, it needs to be replaced.
- Because the air quality varies from place to place, there is no exact service life, generally up to 6 months or more. The standard for replacement is that the minimum air flow is not less than 1.5 times of the tank volume.
- At the end of each fermentation, the air distributor needs to be cleaned.If the nature of the fermentation broth is similar to water, water can be added to the tank and then cleaned by compressed air.If the fermentation broth is sticky or contains fine particles, it is better to remove the air distributor, then unscrew the plug and rinse with water. At the same time, ensure that the small holes are ventilated smoothly.
- Maintenance and servicing of steam systems
It is important to ensure that the steam pressure is constant during use. Steam filter cartridge will also be clogged after a period of use, and the cartridge needs to be replaced. During operation, do not open all steam valves at the same time. This will impact the steam filter element, which will seriously break or leak the element and make it fail.
- Maintenance of dissolved oxygen electrode
- How to replace electrode film and electrolyte
Put the electrode in vertical position and unscrew the old electrode film. Rinse the inner electrode body with water and dry it carefully with cotton paper. Check that there is no electrolyte between the inner electrode body and the stainless steel housing. If there is any residual electrolyte, shake it off gently.
After using for a period of time, if you find that the electrode body silver ring is black, you can use 1000 mesh or more fine sandpaper to polish.
Check O-rings and springs for mechanical damage and replace if needed.
Pour the electrolyte into the membrane to be replaced, with the liquid level controlled below the threads. Adding more electrolyte appropriately can avoid affecting the electrode polarization due to less electrolyte.
Place the electrode in vertical position and screw the membrane gently onto the electrode, pay attention to the principle of "Advance one, retreat two" when screwing the electrode membrane to avoid the membrane being burst due to the excess liquid in the membrane not being discharged in time.Finally the electrode film should be tightened until no O-ring seal color is exposed and the oozing electrolyte is dried with cotton paper.The membrane will be easily tightened due to the sealing effect of the O-ring. If you need to screw it hard or if the process cannot be done easily, it may not be screwed in the correct position.
The electrodes must be repolarized and calibrated after each membrane or electrolyte change (see operating instructions for details).
- Polarization: After replacing new electrolyte or new membrane, it must be continuously powered for more than 7 hours. Polarization before accurate calibration. Polarize first, calibrate later.
- Calibration: Please refer to the oxygen transmitter operating instructions for details.
- Maintenance of solenoid valve
Fault determination, cooling valve failure:
- Open the solenoid valve, the upper surface of the solenoid valve is not magnetic, no cooling water discharge, indicating that the coil is bad.
- Close the solenoid valve, the drain port has cooling water leakage, indicating that the valve spool seal failure.
- Open and close the solenoid valve, the drainage situation remains unchanged,which means the spool is stuck.
- In the case of ensuring the operation of the circulation pump and circulation pipeline, the temperature only drops but not rises the biggest reason is the solenoid valve leakage or spool stuck, the other reason may be the electric heater burned out.
- Other maintenance
- Maintenance of the ball valve: Since the seal inside the ball valve is made of two hemispherical tetrafluoroethylene.After long time use,it may leak between the seal and the spool . Loosen the nut of the ferrule joint at both ends of the valve, and then tighten the cylindrical joint at both ends of the valve.
- Leakage of the ferrule joint: just screw the pressure cap on the joint.
- Maintenance of the discharge valve: Unscrew the valve cover, pull out the spool, and if the seal is damaged, the seal needs to be replaced.
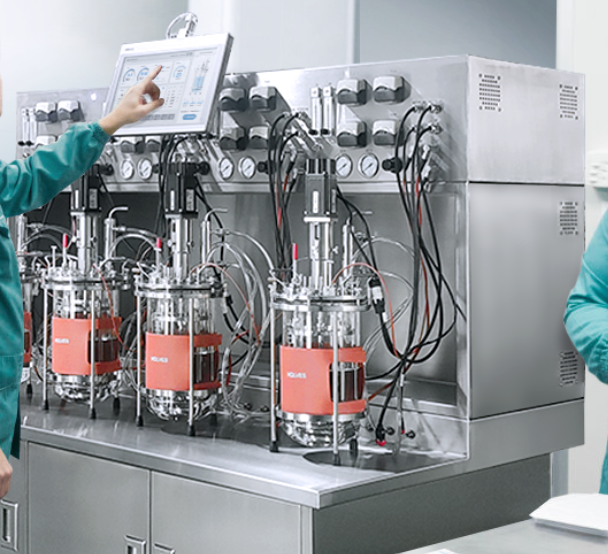