Lactoferrin (LF) is a milk-derived glycoprotein with antimicrobial, immunomodulatory, and iron carrier functions, and is widely used in the fields of infant foods, pharmaceuticals, and functional foods. However, traditional purification processes such as ion exchange chromatography and ultrafiltration have the defects of complicated process, easily damaged protein activity and high production cost. In recent years, ceramic membrane separation technology has become a revolutionary solution for lactoferrin purification due to its unique physicochemical stability and high separation efficiency, providing a more sustainable technological path for industrial production.
Ceramic membranes are porous separation media prepared from inorganic materials such as alumina and zirconia, and their core advantage stems from the material's inherent resistance and the precision of its structural design. Compared to traditional organic polymer membranes, ceramic membranes are able to withstand high temperatures (over 300°C), strong acids and bases (pH 0-14) and organic solvents, making them suitable for the treatment of whey liquids with complex compositions. At the same time, their high mechanical strength allows for frequent high-pressure backwashing operations, which significantly extends membrane service life. In terms of separation performance, ceramic membranes provide molecular weight classification through precise control of pore size, which is particularly suitable for selective retention of lactoferrin. In addition, the smooth and hydrophilic surface of the ceramic membrane reduces membrane contamination caused by protein adsorption, thus maintaining long-term stable separation efficiency.
In the lactoferrin purification process, ceramic membrane filtration technology is usually divided into three stages: pretreatment, ultrafiltration concentration and co-chromatography. Firstly, microfiltration ceramic membranes with a pore size of 0.1-1.2 μm are used to pre-treat the whey raw material, effectively removing fat globules, bacteria and large particles of impurities, while retaining the target components, such as lactoferrin, to reduce the load for subsequent purification. Subsequently, the ultrafiltration ceramic membrane achieves efficient purification through a two-step operation: the primary concentration stage retains lactoferrin and removes impurities such as lactose and small peptides; and the diafiltration stage further enhances the purity of the target proteins to more than 90% through buffer replacement. The study shows that under the optimized conditions of transmembrane pressure of 0.3 MPa and temperature of 25°C, the recovery of lactoferrin can reach 85% and the activity retention rate is over 95%. To further enhance the purity, ceramic membrane filtration is often used as a front-end pretreatment unit for ion exchange chromatography, which significantly reduces the eluent dosage and improves the chromatographic efficiency by reducing the impurity loading of the chromatographic column.
Despite the significant advantages of ceramic membrane filtration technology, its industrialized application still faces the problems of membrane contamination and flux decay. Membrane contamination is mainly caused by protein adsorption and concentration polarization, which can be mitigated by pulsed flow technology, cyclic backwash and intelligent cleaning strategy to enhance membrane flux recovery rate. In the future, with the iteration of ceramic membrane preparation process, the combination of gradient pore size design and anti-contamination coating is expected to achieve more accurate and simultaneous separation of multiple components.
Here is the Holves brand website, https://www.bjholves.com/. Providing different types of industry information, technical knowledge, and solutions, we have developed and produced several new laboratory fermenter, bioreactor, tangential flow filtration system and other equipment to meet your needs from experimental to industrial production.
Ceramic membranes are porous separation media prepared from inorganic materials such as alumina and zirconia, and their core advantage stems from the material's inherent resistance and the precision of its structural design. Compared to traditional organic polymer membranes, ceramic membranes are able to withstand high temperatures (over 300°C), strong acids and bases (pH 0-14) and organic solvents, making them suitable for the treatment of whey liquids with complex compositions. At the same time, their high mechanical strength allows for frequent high-pressure backwashing operations, which significantly extends membrane service life. In terms of separation performance, ceramic membranes provide molecular weight classification through precise control of pore size, which is particularly suitable for selective retention of lactoferrin. In addition, the smooth and hydrophilic surface of the ceramic membrane reduces membrane contamination caused by protein adsorption, thus maintaining long-term stable separation efficiency.
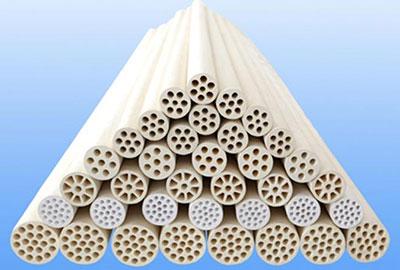
In the lactoferrin purification process, ceramic membrane filtration technology is usually divided into three stages: pretreatment, ultrafiltration concentration and co-chromatography. Firstly, microfiltration ceramic membranes with a pore size of 0.1-1.2 μm are used to pre-treat the whey raw material, effectively removing fat globules, bacteria and large particles of impurities, while retaining the target components, such as lactoferrin, to reduce the load for subsequent purification. Subsequently, the ultrafiltration ceramic membrane achieves efficient purification through a two-step operation: the primary concentration stage retains lactoferrin and removes impurities such as lactose and small peptides; and the diafiltration stage further enhances the purity of the target proteins to more than 90% through buffer replacement. The study shows that under the optimized conditions of transmembrane pressure of 0.3 MPa and temperature of 25°C, the recovery of lactoferrin can reach 85% and the activity retention rate is over 95%. To further enhance the purity, ceramic membrane filtration is often used as a front-end pretreatment unit for ion exchange chromatography, which significantly reduces the eluent dosage and improves the chromatographic efficiency by reducing the impurity loading of the chromatographic column.
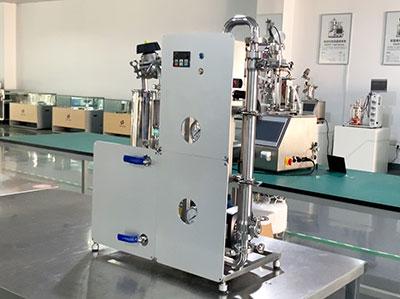
Despite the significant advantages of ceramic membrane filtration technology, its industrialized application still faces the problems of membrane contamination and flux decay. Membrane contamination is mainly caused by protein adsorption and concentration polarization, which can be mitigated by pulsed flow technology, cyclic backwash and intelligent cleaning strategy to enhance membrane flux recovery rate. In the future, with the iteration of ceramic membrane preparation process, the combination of gradient pore size design and anti-contamination coating is expected to achieve more accurate and simultaneous separation of multiple components.
Here is the Holves brand website, https://www.bjholves.com/. Providing different types of industry information, technical knowledge, and solutions, we have developed and produced several new laboratory fermenter, bioreactor, tangential flow filtration system and other equipment to meet your needs from experimental to industrial production.