The requirements of the bioreactor for feeding and feeding acid-base in the process determine the equipment's high requirements for the control precision of the peristaltic pump. There are a variety of ways for the stepper motor to control the peristaltic pump, which are usually used in the bioreactor by pulse, analog quantity and RS-485 communication.
In order to study the intuitive influence of these three control methods on the control precision of the peristaltic pump, HOLVES specially conducted a comparative experiment.
Pulse volume peristaltic pump (calibrated before the test)
Analog peristaltic pump (calibrated before testing)
RS-485 communication peristaltic pump (calibrated before the test)
No.16 silicone tube
Graduated cylinder 1 (Volume: 20mL, Accuracy: 0.5mL)
Graduated cylinder 2 (Volume: 50mL, Accuracy: 1mL)
Beaker
Pure water
(2) Experimental steps
① Insert the No. 16 silicone tube into the center of the peristaltic pump roller, and fasten the cover to fix the peristaltic pump;
② Place both the liquid inlet and outlet ends of the silicone tube in a beaker filled with pure water;
③ Set the manual speed to discharge the air in the silica gel tube. When the pure water is pumped to the liquid outlet of the silica gel tube that is the red line position below, stop the pumping liquid;
④ Place the liquid outlet end in the measuring cylinder of the appropriate range, and pay attention to not sticking to the wall to prevent the liquid hanging on the wall from affecting the experimental results;
⑤ After setting the speed of the peristaltic pump and the volume of the target pump liquid on the equipment, the peristaltic pump is run, and the running time is recorded;
⑥ After the end of the pump fluid, observe and record the actual volume of the pump fluid;
⑦ Repeat the above operation, test and record the operation data of all peristaltic pumps.
During the course of the experiment, no further calibrations can be performed, regardless of the difference in the pumped fluid volume.
When reading the volume of the pumped liquid, place the graduated cylinder on a flat table so that the line of sight is level with the lowest part of the liquid concave surface in the graduated cylinder.
As can be seen from the data in the table, once the speed and pump output are changed, the peristaltic pumps controlled by different driving methods will have different results. Among the three drive modes, the RS-485 communication mode has the best control accuracy, followed by the pulse, and the analog quantity has the largest error.
In order to study the intuitive influence of these three control methods on the control precision of the peristaltic pump, HOLVES specially conducted a comparative experiment.
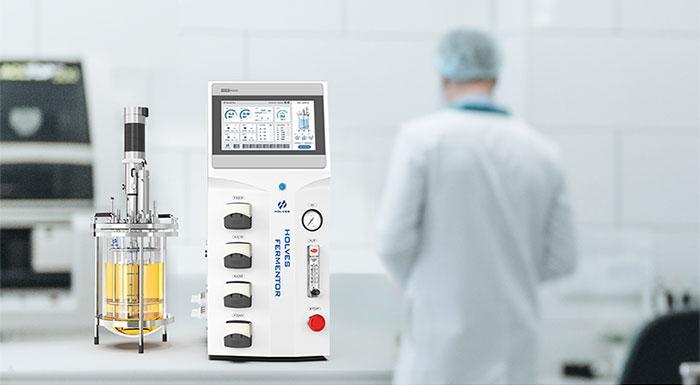
First of all, we must first understand what these three driving methods are?
- Pulse quantity: A digital quantity whose value always alternates between0(low level) and 1(high level). The number of alternating pulses per second is called frequency. Pulse volume is mainly used for position control, speed control and torque control of stepper motor and servo motor.
- Analog quantity: It is a continuous signal quantity such as voltage and current. An analog signal is a signal whose amplitude changes continuously with time, after sampling and quantization, it is a digital quantity. The analog quantity is mostly non-electric quantity, and PLC can only deal with digital quantity and electric quantity, so to realize the conversion between them requires a sensor to convert the analog quantity into digital electric quantity. If this quantity of electricity is not standard, the non-standard quantity of electricity needs to be converted into a standard electrical signal through a transmitter. In addition, an analog input unit (AD) is required to convert these standard electrical signals into digital signals.
- RS-485: It is a serial data interface standard. In order to expand the communication capability of the application range, multi-point and two-way communication capability is added, that is, it allows up to 32 receivers to be connected on a balanced bus, and also increases the transmitter's The drive capability and communication collision protection features extend the common-mode range of the bus through differential transmission.
- Experimental design
- Experimental methods and steps
Pulse volume peristaltic pump (calibrated before the test)
Analog peristaltic pump (calibrated before testing)
RS-485 communication peristaltic pump (calibrated before the test)
No.16 silicone tube
Graduated cylinder 1 (Volume: 20mL, Accuracy: 0.5mL)
Graduated cylinder 2 (Volume: 50mL, Accuracy: 1mL)
Beaker
Pure water
(2) Experimental steps
① Insert the No. 16 silicone tube into the center of the peristaltic pump roller, and fasten the cover to fix the peristaltic pump;
② Place both the liquid inlet and outlet ends of the silicone tube in a beaker filled with pure water;
③ Set the manual speed to discharge the air in the silica gel tube. When the pure water is pumped to the liquid outlet of the silica gel tube that is the red line position below, stop the pumping liquid;
④ Place the liquid outlet end in the measuring cylinder of the appropriate range, and pay attention to not sticking to the wall to prevent the liquid hanging on the wall from affecting the experimental results;
⑤ After setting the speed of the peristaltic pump and the volume of the target pump liquid on the equipment, the peristaltic pump is run, and the running time is recorded;
⑥ After the end of the pump fluid, observe and record the actual volume of the pump fluid;
⑦ Repeat the above operation, test and record the operation data of all peristaltic pumps.
- Notes
During the course of the experiment, no further calibrations can be performed, regardless of the difference in the pumped fluid volume.
When reading the volume of the pumped liquid, place the graduated cylinder on a flat table so that the line of sight is level with the lowest part of the liquid concave surface in the graduated cylinder.
- Experimental data analysis
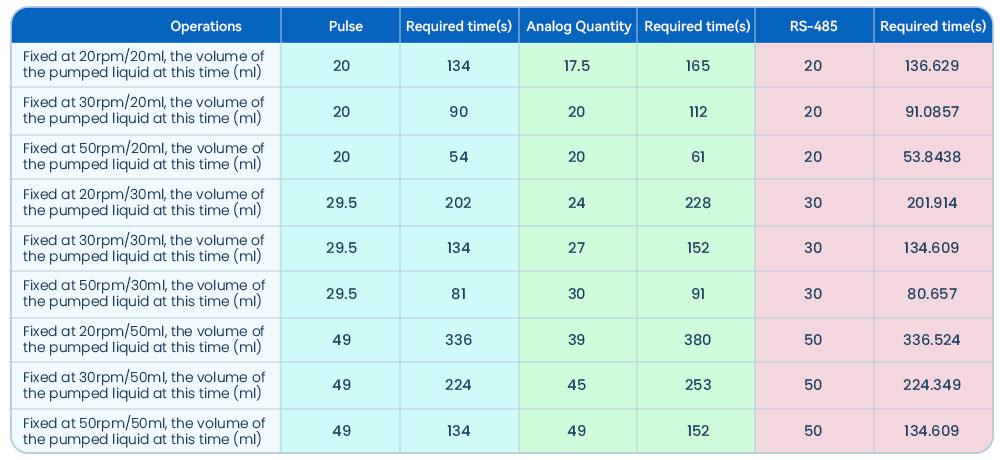
(Stepper motor drive precision test)
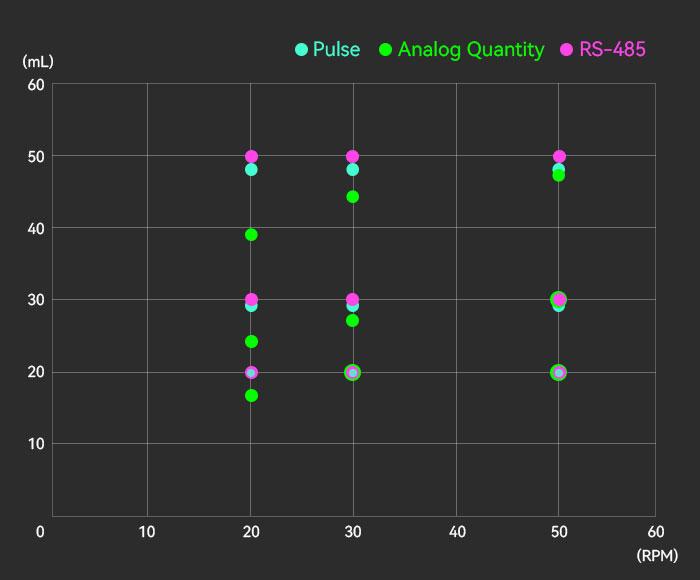
(Precision test scatter diagram)
As can be seen from the data in the table, once the speed and pump output are changed, the peristaltic pumps controlled by different driving methods will have different results. Among the three drive modes, the RS-485 communication mode has the best control accuracy, followed by the pulse, and the analog quantity has the largest error.
Advantages of RS-485 Communication
In addition to giving the peristaltic pump high control accuracy, the RS-485 communication method also has the following advantages:
①The system runs stably—use the dedicated communication bus to connect the concentrator and the master station safely and reliably. Unless the device interface hardware is damaged, or the bus line is disconnected, the bus meter reading system will always maintain a good communication effect and success rate of reading.
②High communication rate - due to the use of a dedicated wired communication line connection, there is no other signal on the line except for communication signals. And the attenuation after the external interference signal is coupled to the line is very large, so the concentrator can communicate with the master station at a higher rate.
③Anti-interference - The RS-485 bus channel is a dedicated communication channel. The shielding added to the communication cable can effectively ensure the communication effect, so it has strong anti-spatial interference performance.
The HOLVES bioreactor has basically been updated to the RS-485 communication mode in the driving mode of the stepper motor, which effectively improves the control performance of the peristaltic pump during the fermentation process.
①The system runs stably—use the dedicated communication bus to connect the concentrator and the master station safely and reliably. Unless the device interface hardware is damaged, or the bus line is disconnected, the bus meter reading system will always maintain a good communication effect and success rate of reading.
②High communication rate - due to the use of a dedicated wired communication line connection, there is no other signal on the line except for communication signals. And the attenuation after the external interference signal is coupled to the line is very large, so the concentrator can communicate with the master station at a higher rate.
③Anti-interference - The RS-485 bus channel is a dedicated communication channel. The shielding added to the communication cable can effectively ensure the communication effect, so it has strong anti-spatial interference performance.
The HOLVES bioreactor has basically been updated to the RS-485 communication mode in the driving mode of the stepper motor, which effectively improves the control performance of the peristaltic pump during the fermentation process.