Most of the bioreactors used for fermentation are stirring type, and dissolved oxygen is an important parameter of biological metabolic reaction. The supply of oxygen has a great impact on the growth of bacteria and the accumulation of metabolites, which determines the yield of metabolites. Therefore, the study of oxygen supply is of great significance to the optimization of biological reaction process management and the amplification of the process. At the same time, reasonable oxygen supply is also important for saving consumption.
In the process of aerobic fermentation, cells need molecular oxygen as the electron acceptor at the end of the electron transfer system of the respiratory chain, and finally combine with hydrogen ions to form water and release a lot of energy for cell growth and synthesis. The oxygen diffusion rate in the medium may be a factor limiting the respiration process.
The proper supply of oxygen in the process of biological culture is a necessary condition to ensure the good growth of bacteria and the high production of products. Insufficient oxygen will lead to abnormal metabolism and reduced output, but too high dissolved oxygen and too fast cell growth will also be detrimental to biosynthesis. Dissolved oxygen is the result of the contradictory balance between oxygen supply and oxygen demand.
If the outside world cannot supply oxygen in time, the dissolved oxygen in the water can only maintain the normal respiration of microbial cells in the culture medium, and then it will be exhausted. Therefore, it is necessary to continuously inject sterile air into the bioreactor system and further disperse it through stirring to maintain a moderate dissolved oxygen concentration in the hair culture medium, so as to ensure the normal growth of microorganisms and the formation of required metabolites.
Through the study on the dissolved oxygen performance of the stirred bioreactor and the actual production situation, it is concluded that the multi-layer disc turbine agitator can be used for smaller volume; For large size, the disc turbine agitator is retained at the bottom layer, and the axial flow impeller is used to replace the upper turbine agitator to form a reasonable combination of agitators. In this way, the advantages of the turbine agitator for gas dispersion can be brought into play, and the axial flow agitator can be supplemented to enhance the circulation in the tank and improve the dissolved oxygen.
Of course, the selection of agitator type should be careful. The data and production experience provided here are far from meeting the needs of actual production. Therefore, the data must be obtained through small simulation tests, and the speed and other parameters of the agitator must be determined according to the amplification principle.
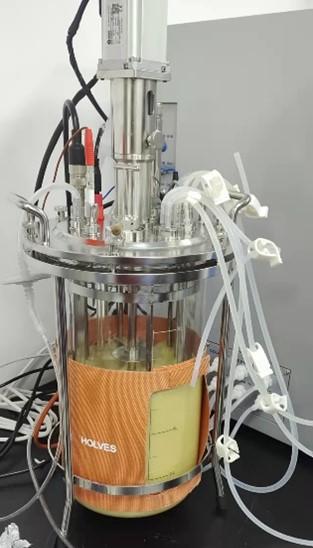
In the process of aerobic fermentation, cells need molecular oxygen as the electron acceptor at the end of the electron transfer system of the respiratory chain, and finally combine with hydrogen ions to form water and release a lot of energy for cell growth and synthesis. The oxygen diffusion rate in the medium may be a factor limiting the respiration process.
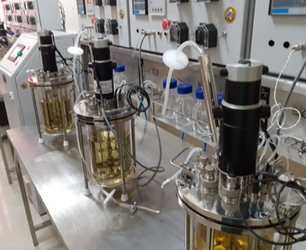
The proper supply of oxygen in the process of biological culture is a necessary condition to ensure the good growth of bacteria and the high production of products. Insufficient oxygen will lead to abnormal metabolism and reduced output, but too high dissolved oxygen and too fast cell growth will also be detrimental to biosynthesis. Dissolved oxygen is the result of the contradictory balance between oxygen supply and oxygen demand.
If the outside world cannot supply oxygen in time, the dissolved oxygen in the water can only maintain the normal respiration of microbial cells in the culture medium, and then it will be exhausted. Therefore, it is necessary to continuously inject sterile air into the bioreactor system and further disperse it through stirring to maintain a moderate dissolved oxygen concentration in the hair culture medium, so as to ensure the normal growth of microorganisms and the formation of required metabolites.
Through the study on the dissolved oxygen performance of the stirred bioreactor and the actual production situation, it is concluded that the multi-layer disc turbine agitator can be used for smaller volume; For large size, the disc turbine agitator is retained at the bottom layer, and the axial flow impeller is used to replace the upper turbine agitator to form a reasonable combination of agitators. In this way, the advantages of the turbine agitator for gas dispersion can be brought into play, and the axial flow agitator can be supplemented to enhance the circulation in the tank and improve the dissolved oxygen.
Of course, the selection of agitator type should be careful. The data and production experience provided here are far from meeting the needs of actual production. Therefore, the data must be obtained through small simulation tests, and the speed and other parameters of the agitator must be determined according to the amplification principle.